At Lynx Siding, we take pride in our commitment to best practices and adherence to architect and building envelope requirements. In this case study, we were called by a general contractor to provide an expert analysis of siding installation mistakes made by a previous contractor. Using marked and numbered details in the accompanying pictures, we highlight key issues and explain how they should have been properly addressed.
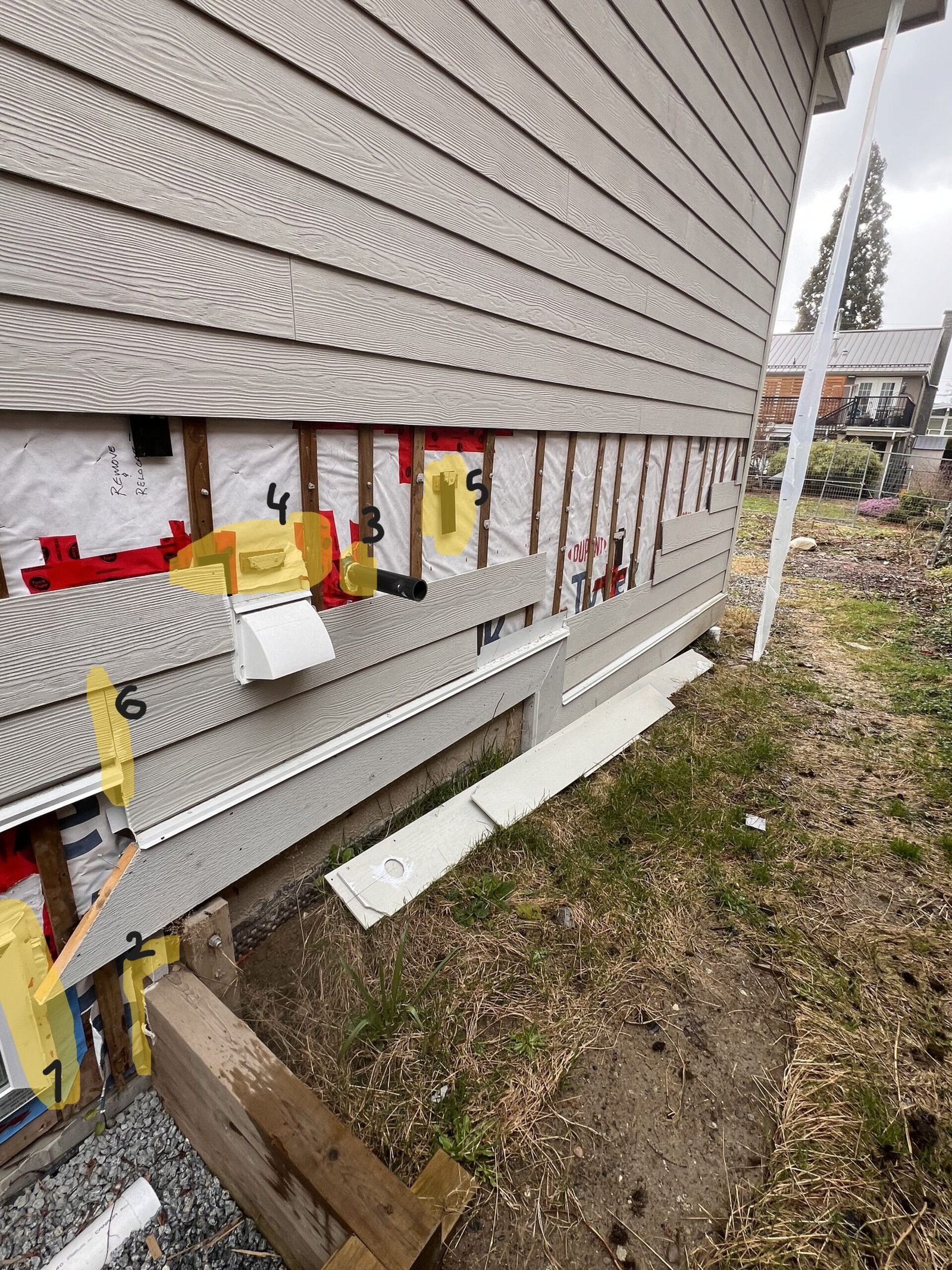
Picture 1: Window Preparation and Waterproofing Issues
Detail #1 – The window flanges on the left and right sides must be overlapped by the building wrap. Proper window installation requires:
- Opening preparation with building wrap (or self-adhesive (SA) membrane) on the left, top, and right sides, and SA membrane on the bottom.
- A metal flashing over the top of the window, installed directly over the building wrap.
- The field building wrap overlapping three sides (left, top, right), while the bottom piece of opening preparation must overlap the field building wrap—following the shingle-out principle.
Detail #2 – SA membrane flashing must be applied both horizontally and vertically over the field building wrap and wood retaining wall, with a bead of polyurethane sealant on the edges. This prevents water infiltration behind the building wrap, which could lead to sheathing damage.
Detail #3 – Similar to Detail #1, objects penetrating the wall—such as PVC pipes, electrical outlets, and ducts—must follow the shingle-out principle to ensure proper water drainage and prevent leaks.
Detail #4 –
- No bug screen is installed, leaving space for insects to nest behind the siding.
- A plywood strapping piece is fastened horizontally, which is incorrect.
- The previous installer used a very small piece of fiber cement siding over an exhaust fan, which is a poor practice.
Detail #5 – Although flashing was properly used behind a butt joint, the application was incorrect. If a butt joint does not meet on a strapping, additional strapping should be provided for support. The best practice is to plan siding layout in advance to align with pre-installed strapping.
Detail #6 – End dams are usually installed at the tops of windows and doors to direct water away. However, in this case, a butt joint was positioned directly above an end dam, creating a risk for water penetration. Best practice is to install a single, longer piece of siding and notch it to avoid joints over end dams.
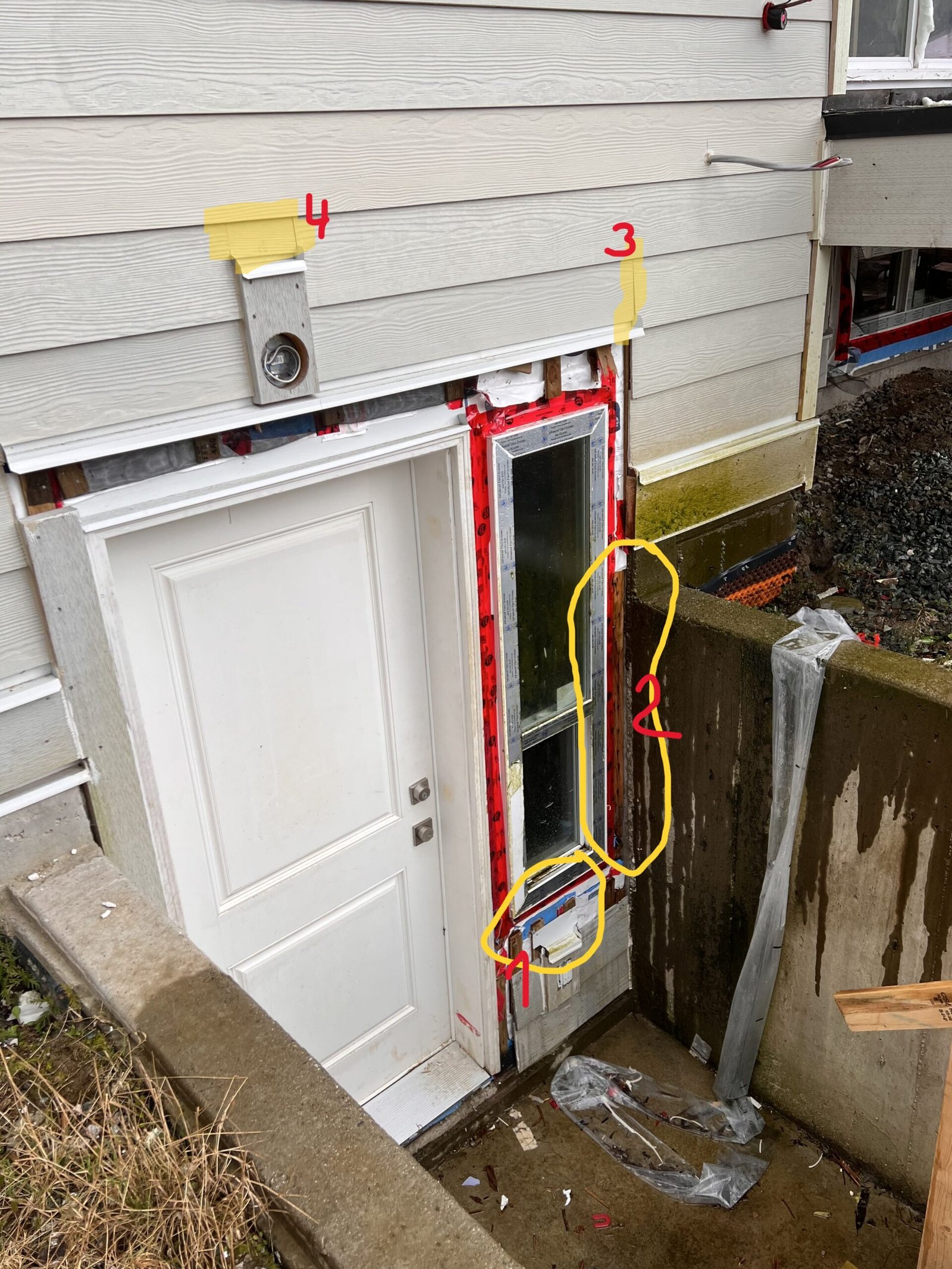
Picture 2: Drainage and Flashing Errors
Detail #1 – The bottom flange of the window must not be sealed, as a weeping gap is necessary for condensation drainage. Additionally, the metal flashing above the outlet box should be installed as a through-wall flashing, meaning:
- The building wrap must overlap the flashing.
- Strapping must be installed over the metal flashing to maintain proper water drainage.
Detail #2 – This has the same issue as Detail #2 from Picture 1. An SA membrane should be applied to transition from the building wrap to concrete, with a bead of polyurethane sealant on the edges.
Details #3 and #4 – Both show the same issue as Detail #6 from Picture 1—poor butt joint placement over an end dam.
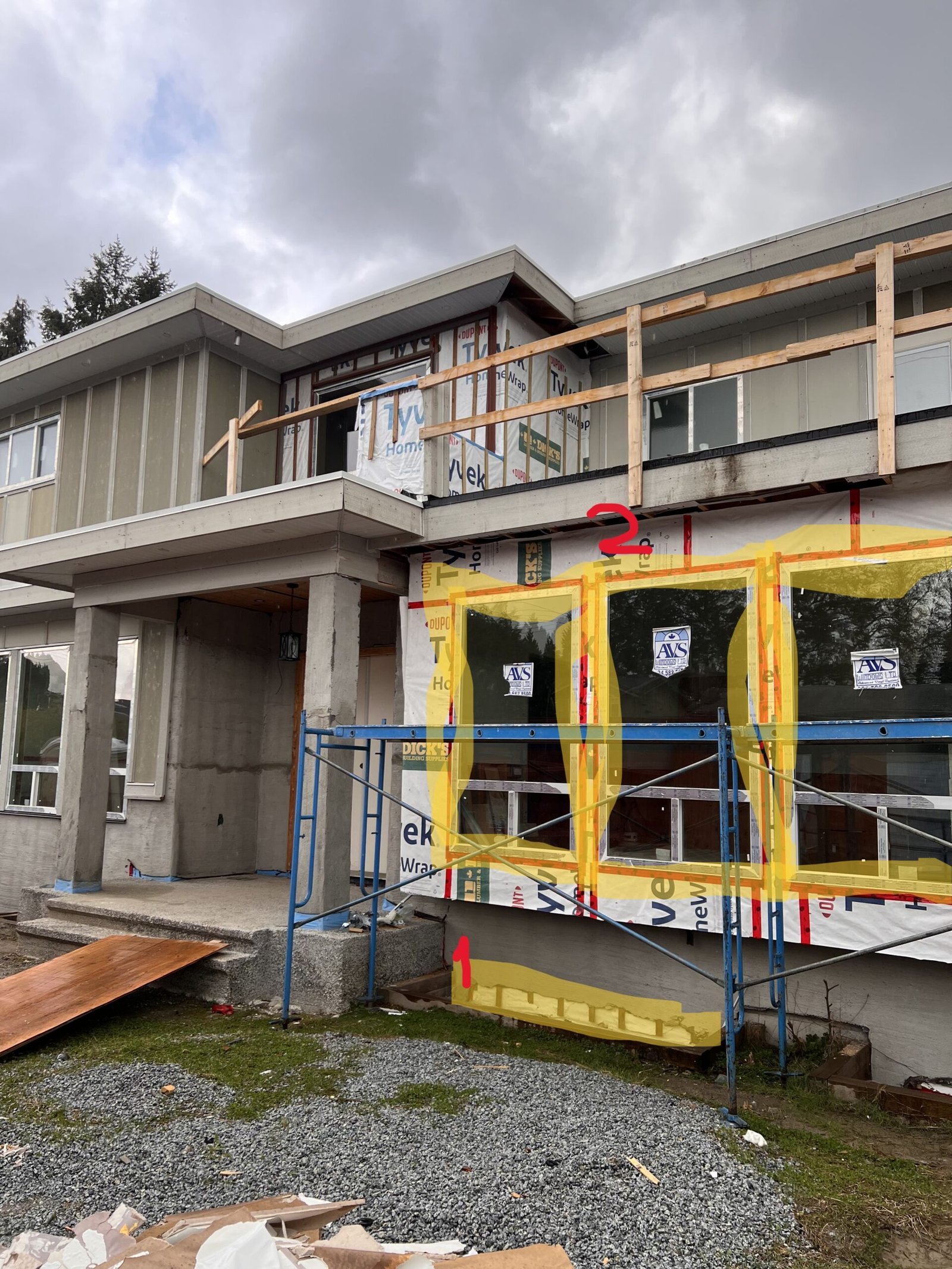
Picture 3: Strapping and Window Preparation Errors
Detail #1 – Strapping for stucco siding was incorrectly installed. Stucco requires strapping at 8-inch on-center (O.C.) spacing to provide adequate support.
Detail #2 – Same issue as Detail #1 from Picture 1—improper opening preparation and missing field building wrap overlap. Additionally, the bottom flange of the window must remain unsealed.
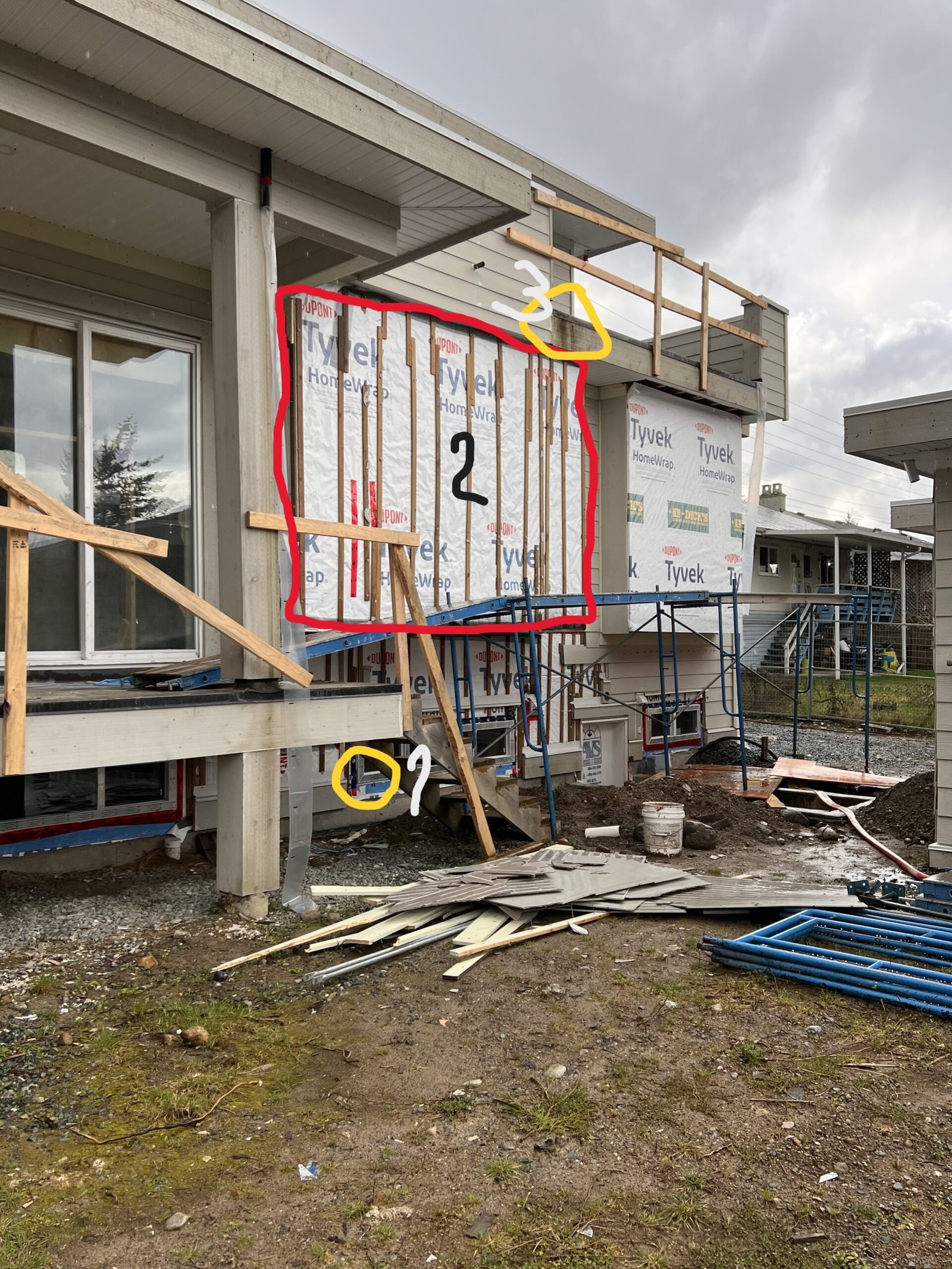
Picture 4: Good and Bad Examples
Detail #1 – A proper window installation example. The plastic window shim creates the necessary gap for condensation drainage – a weeping gap.
Detail #2 – Two vertical strapping pieces are nailed side by side. This raises a concern: one of them is likely not nailed into a stud. If no stud is available, strapping should not be doubled unless the sheathing is at least 3/4-inch thick.
Detail #3 – A bad cap flashing installation is evident from the wood stain on the trim. The metal cap flashing was installed too tightly against the wood, preventing water from dripping off properly. This issue is seen throughout the fascia trim at the roof and parapet walls.
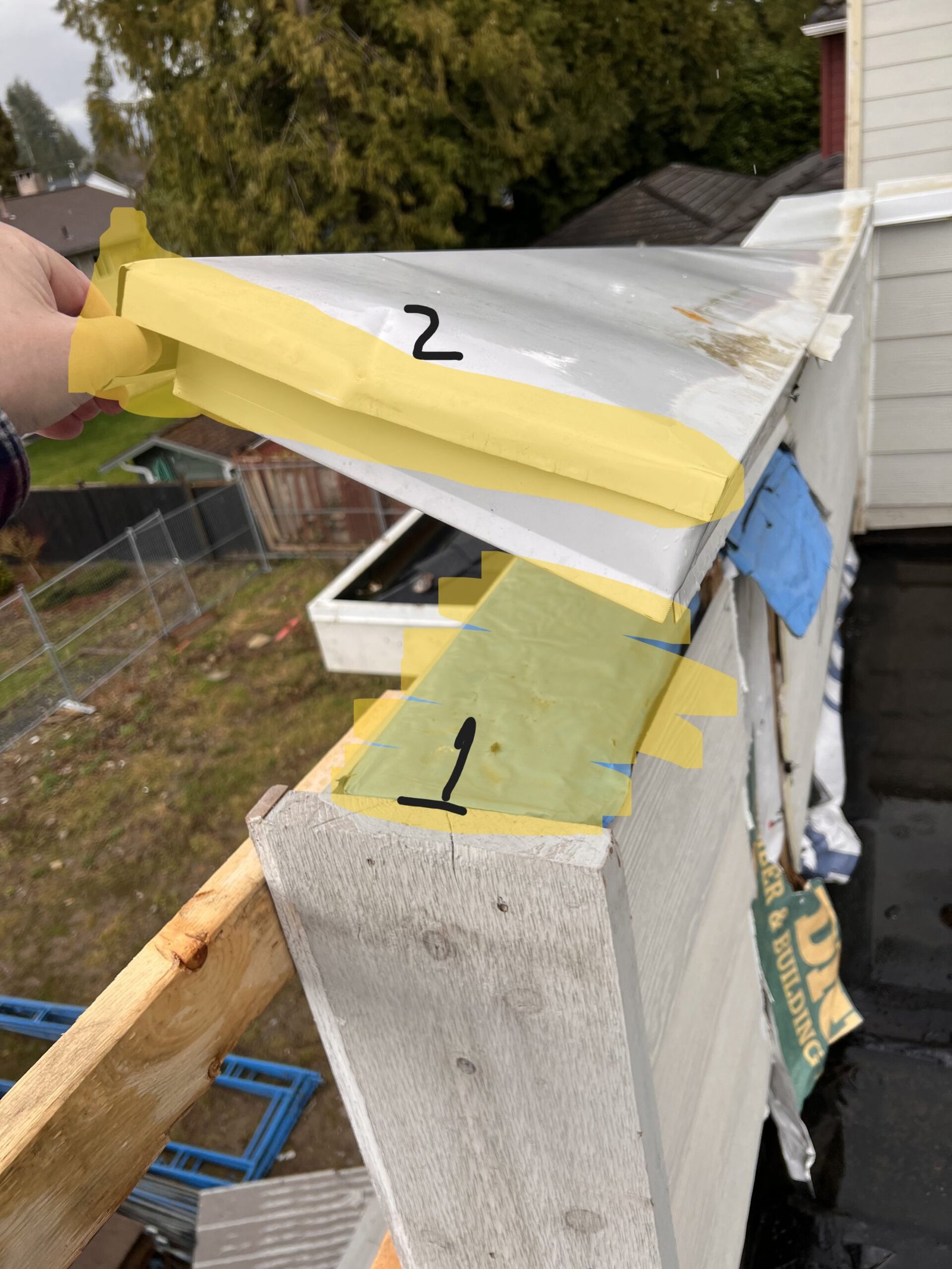
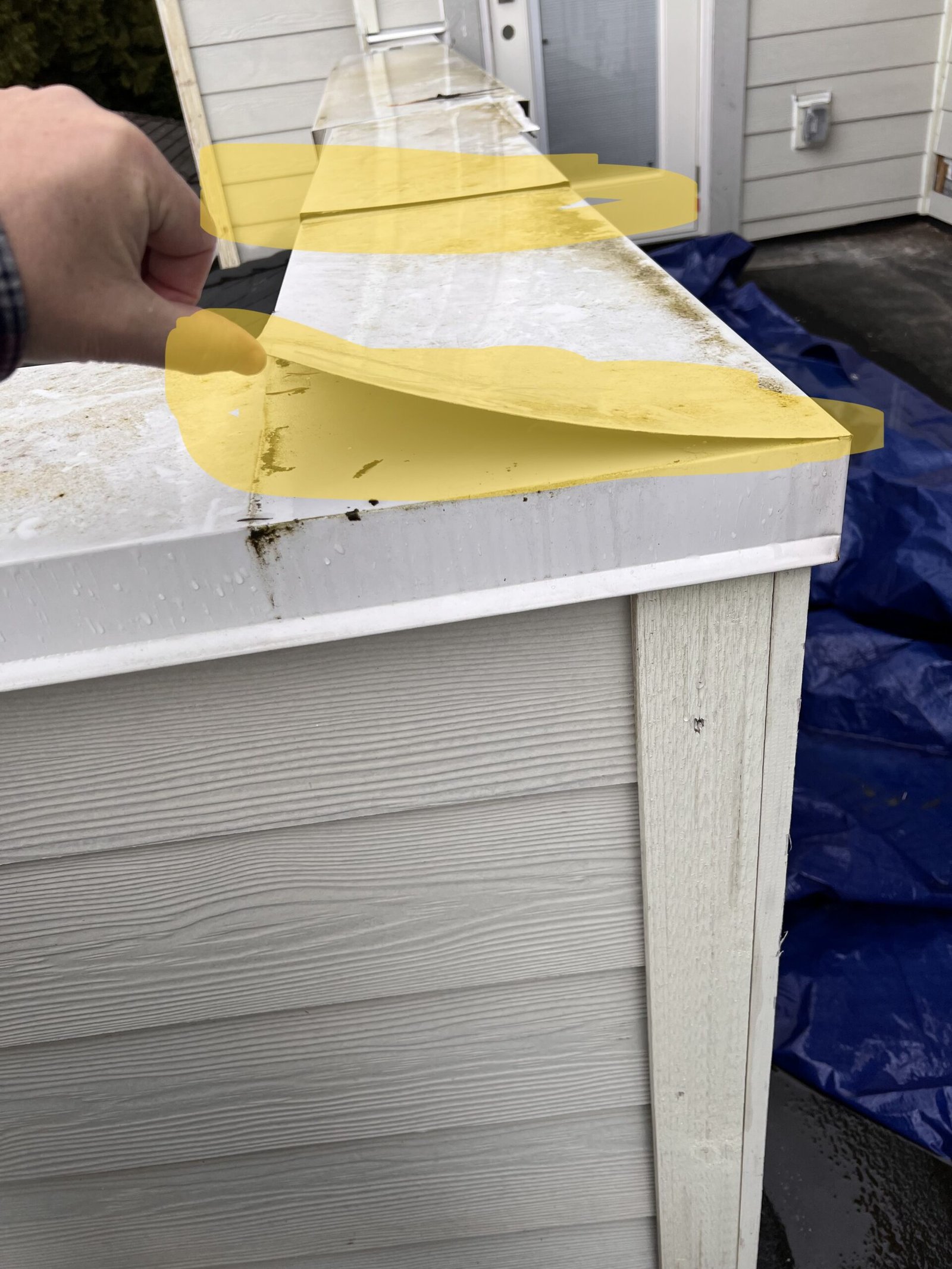
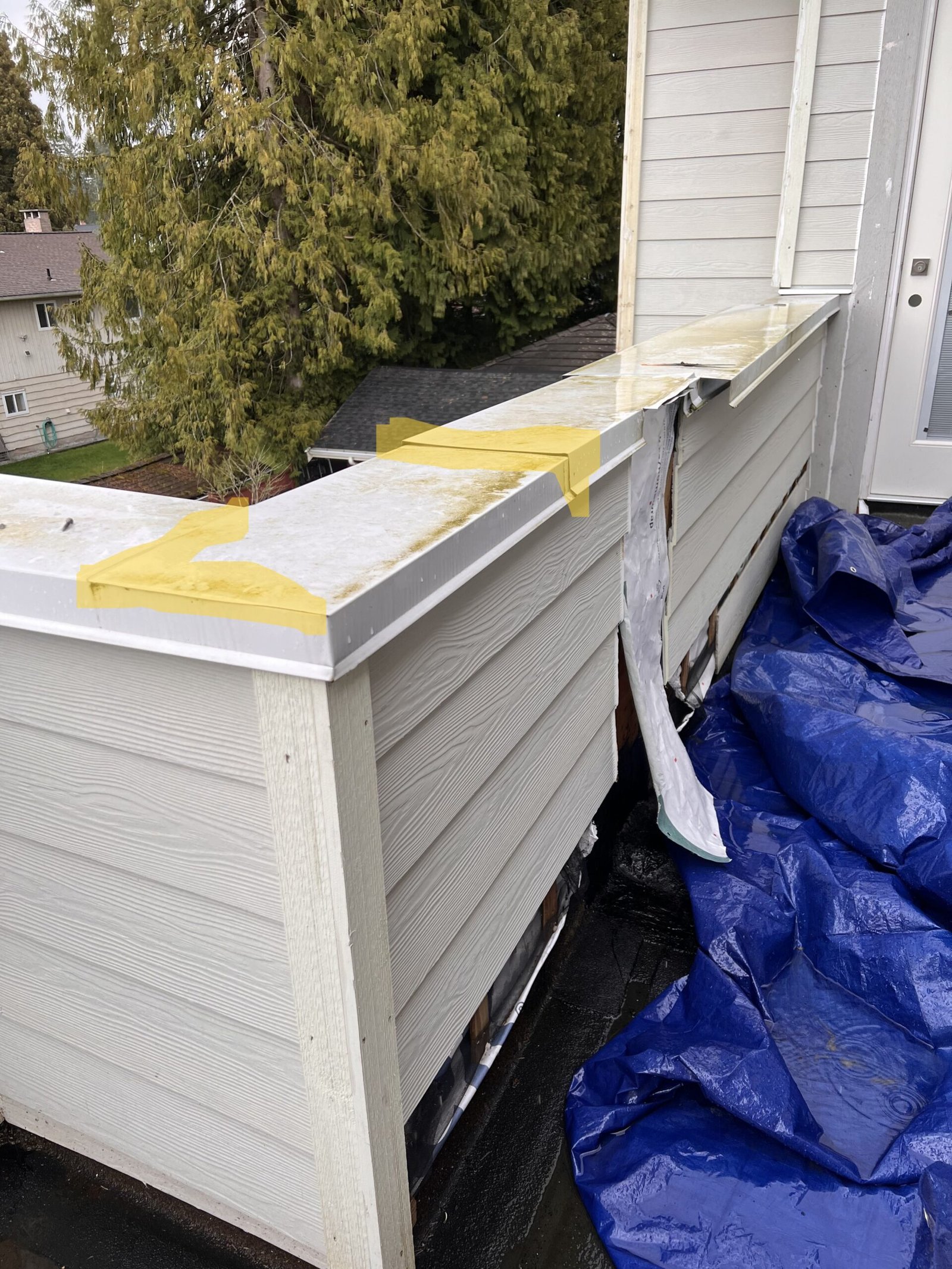
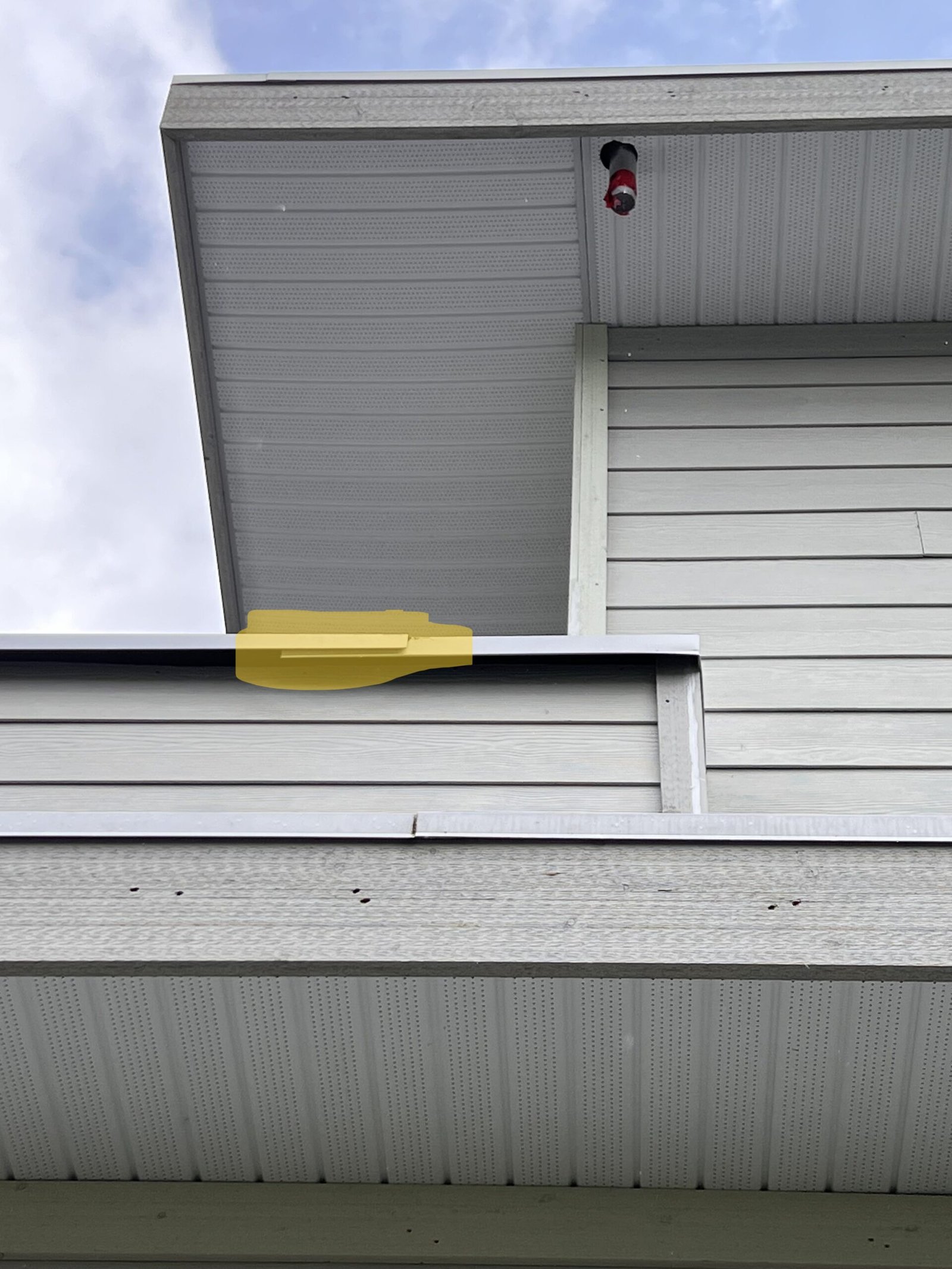
Pictures 5–8: Metal Cap Flashing Issues
Detail #1 (Picture 5) – Incorrect preparation for metal cap flashing. The correct approach includes:
- A 1/2-inch per foot slope directed inward, typically achieved using beveled cedar siding.
- High-temperature (HT) SA membrane flashing.
- The SA membrane should overlap the strapping, rather than being covered by it, to ensure proper water shedding.
Detail #2 (Picture 5) – The metal cap flashing must be securely installed using:
- Metal clips interlocked along the drip edge or at the joints using S-lock or standing seam connections.
- Alternatively, screws with rubber gaskets (though less desirable) may be used on the sides of the cap flashing.
Additionally, in Pictures 5–8, the metal flashing contractor failed to properly fabricate the flashing corners and did not install S-lock or standing seam connections at each joint.
Conclusion
This case study highlights common yet critical mistakes made by inexperienced and low-priced siding contractors. At Lynx Siding, we strictly adhere to best industry practices, ensuring all installations follow the highest standards for waterproofing, durability, and long-term performance. Proper material selection, meticulous installation, and attention to detail are crucial to prevent costly repairs and potential structural damage. Our expertise guarantees that your siding is installed the right way—the first time.
Contact us today for a free quote for your next project!